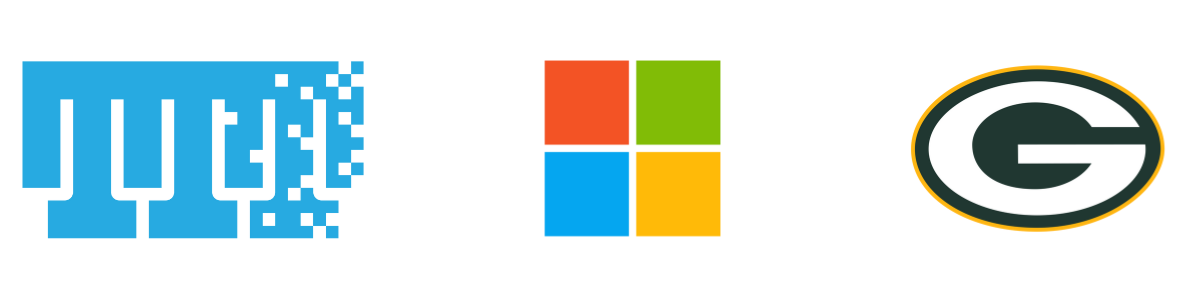
MaintainVO
Automated PM and Work Order Management
- Stay informed with an all-encompassing Maintenance Dashboard
- Create, manage, and assign PMs and work orders
- Manage parts lists, documents, specs, historical records, and more in one accessible location
- Information is constantly being added to create detailed, up-to-date reports and records